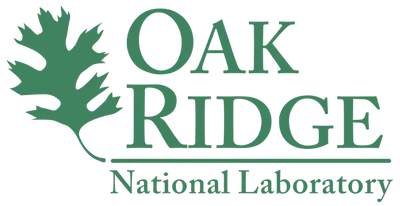
Introduction
In summer 2019, I joined Oak Ridge National Laboratory (ORNL) in Oak Ridge, TN as an intern under the supervision of Dr. Mohammed Olama.
This was my second time as an intern at ORNL, having previously completed an internship at the National Transportation Research Center (NTRC) under the supervision of its current director Dr. Robert Wagner when I was in middle school, so the environment was a familiar one.
HVAC Control Project
Background
Dr. Olama’s research team is currently working on a project to develop strategies to control the transmission/distribution of power to appliances in residential buildings (e.g. residential HVAC systems and water heaters). One of the proposed control schemes used in his team’s project is model-free control (MFC), a form of control effective at the low time scales necessary for this application. As detailed mathematical models of the system being controlled are unnecessary when using MFC, MFC is also relatively easy to implement.
My project specifically involved the training of neural networks to predict the effectiveness of MFC for controlling the distribution of power to residential building HVAC systems, subject to certain power and external temperature constraints. The HVAC systems in turn control the internal temperatures of the buildings.
Dr. Olama’s research team supplied me with Matlab code that uses a MFC algorithm to control the internal temperature of 100 identical buildings over a given duration. The code takes two sets of data as input:
- A time series of the total power available to cool all 100 buildings (a “power profile”); and
- A time series of the temperature outside the 100 buildings (a “temperature profile”).
The code uses these two inputs, along with a desired “ideal” temperature (the ‘setpoint"), to generate a time series of the internal temperature for each building using MFC (the “temperature response”). The goal of the MFC control scheme is to keep the internal temperature of the 100 buildings at each timestep within a certain “comfort band” of the setpoint (e.g., within ±1.5 °C of a 23 °C setpoint) while also using all of the available total cooling power at that timestep.
Motivation
This MFC code is implemented in the overarching residential appliance control project; however, there was one issue that arose in regards to how the MFC is implemented. In the project, it is necessary to know whether MFC will be feasible for a given set of power and weather profiles and only implement MFC if it will yield “well-controlled” results. Specifically, a “well-controlled” temperature response is one in which the internal temperature of each of the 100 buildings remains inside the comfort band for most of the control duration.
Dr. Olama’s research team desired to be able to predict how well a set of 100 identical buildings under a given combination of power profile and temperature profile constraints could be controlled using the MFC algorithm. To address this issue, my project involved training neural networks that could accomplish the prediction.
Work
Training Data Generation
I generated the data to train these neural networks by running the MFC code using a wide variety of power and temperature profiles (nearly 70,000 unique combinations) as inputs. The power profiles used to train the neural networks included simulated daily power usage data for Atlanta office and apartment buildings over 30 years, and the temperature profiles included daily external temperature measured at Las Vegas Airport over one year.
A numerical “rating” from 0 to 10 based on the corresponding MFC internal temperature output was generated for each combination of power and temperature profiles. A rating of 0 implies that the internal temperatures were outside of the comfort band at nearly all timesteps, and a rating of 10 implies that the internal temperatures were inside the comfort band at nearly all timesteps. The training process is visualized in fig. 1. I used these 70,000 unique combinations of power and temperature profiles, along with the rating of the output, to train the neural networks.
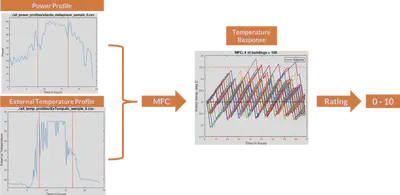
One may supply a description of a power profile and a description of a temperature profile to the neural network to generate a predicted rating of how well the internal temperature of the 100 buildings would be controlled if the MFC control simulation was run using those power and temperature profiles.
Results
Based on our results using a test dataset that we had set aside before the training, we found that the neural networks were able to accurately predict the efficiency of MFC to control. That is, the neural networks" predictions of the efficiency rating for a given set of starting conditions (power and temperature profiles) mostly matched the actual rating obtained by running the MFC code using those starting conditions.
While training these neural networks, I worked on some other methods to aid in the prediction of effectiveness of the MFC algorithm. Using Matlab, I trained several regression models on the same data used to train the neural networks. In addition, I applied k-means clustering on the power and temperature profile data to aid in recognizing which power and temperature data yielded more “well-controlled” results.
Takeaways
- Model-free control
- Neural network training
- Matlab neural network / regression apps
- K-means clustering
Conclusion
I enjoyed the experience I had during my internship, and I am grateful to Dr. Olama and his research team for the experience. Attending the weekly meetings of the research team exposed me to other aspects of the main project that the team was working on that I found quite interesting, such as the application of game theory techniques for control and energy market modelling; this gave me a taste of the other aspects of the overarching project apart from those dealing with the project that I personally worked on. Understanding the logistics behind the kind of projects undertaken at a national laboratory was also insightful.
My work on this project resulted in the publication of a paper by Dr. Olama, my colleague Kadir Amasyali, and myself for the Eleventh Conference on Innovative Smart Grid Technologies (ISGT 2020) in February 2020. The abstract for the paper may be found on this page.